APQP (उन्नत उत्पाद गुणवत्ता योजना) चरण, उदाहरण
APQP (उन्नत उत्पाद गुणवत्ता योजना), स्पैनिश "एडवांस्ड प्रोडक्ट क्वालिटी प्लानिंग" में होने के कारण, यह उद्योग में उत्पादों को विकसित करने के लिए उपयोग की जाने वाली प्रक्रियाओं और तकनीकों का ढांचा है, विशेष रूप से ऑटोमोटिव।.
जटिल उत्पाद और आपूर्ति श्रृंखलाएं विफलता की कई संभावनाएं पेश करती हैं, खासकर जब नए उत्पाद लॉन्च किए जाते हैं। APQP उत्पादों और प्रक्रियाओं के डिजाइन के लिए एक संरचित प्रक्रिया है, जिसका उद्देश्य नए उत्पादों या प्रक्रियाओं के साथ ग्राहकों की संतुष्टि की गारंटी देना है.
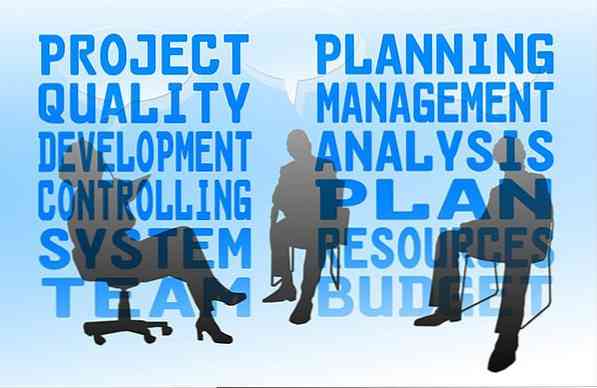
यह दृष्टिकोण एक नए उत्पाद या प्रक्रिया में परिवर्तन से जुड़े जोखिमों को कम करने के लिए उपकरणों और विधियों का उपयोग करता है.
इसका उद्देश्य उत्पाद गुणवत्ता आवश्यकताओं की एक मानकीकृत योजना का उत्पादन करना है, जो आपूर्तिकर्ताओं को एक उत्पाद या सेवा को डिजाइन करने की अनुमति देता है जो ग्राहक को संतुष्ट करता है, विभिन्न गतिविधियों के बीच संचार और सहयोग को सुविधाजनक बनाता है।.
APQP प्रक्रिया में, एक बहुक्रियाशील टीम का उपयोग किया जाता है, जिसमें विपणन, उत्पाद डिजाइन, क्रय, उत्पादन और वितरण शामिल है। इस प्रक्रिया का उपयोग जनरल मोटर्स, फोर्ड, क्रिसलर और इसके आपूर्तिकर्ताओं द्वारा अपने उत्पाद विकास प्रणाली के लिए किया जाता है.
सूची
- 1 चरण
- 1.1 चरण 1: कार्यक्रम की योजना और परिभाषा
- 1.2 चरण 2: उत्पाद का डिजाइन और विकास
- 1.3 चरण 3: उत्पाद निर्माण प्रक्रिया का डिजाइन और विकास
- 1.4 चरण 4: प्रक्रिया और उत्पाद सत्यापन
- 1.5 चरण 5: लॉन्च, मूल्यांकन और निरंतर सुधार
- 2 उदाहरण
- 2.1 APQP को कहां शामिल करना है
- २.२ उद्योग जो इसका उपयोग करते हैं
- 3 संदर्भ
चरणों
APQP विकास प्रक्रिया में एक गाइड के रूप में और आपूर्तिकर्ताओं और ऑटोमोटिव कंपनियों के बीच परिणामों को साझा करने के मानक तरीके के रूप में कार्य करता है। इसमें पाँच चरण होते हैं:
चरण 1: कार्यक्रम की योजना और परिभाषा
जब ग्राहकों की मांग के लिए एक नए उत्पाद की शुरूआत या किसी मौजूदा संशोधन की आवश्यकता होती है, तो योजना उत्पाद का डिजाइन या नया स्वरूप के बारे में चर्चा से पहले ही एक केंद्रीय विषय बन जाता है।.
इस चरण में, योजना ग्राहक की जरूरतों और उत्पाद की अपेक्षाओं को समझने का प्रयास करती है.
नियोजन गतिविधियों में ग्राहक को क्या चाहिए और उत्पाद की विशेषताओं पर चर्चा करने के लिए इस जानकारी का उपयोग करके परिभाषित करने के लिए आवश्यक डेटा एकत्र करना शामिल है.
फिर आप उत्पाद को निर्दिष्ट करने के लिए आवश्यक गुणवत्ता कार्यक्रम को परिभाषित कर सकते हैं.
इस कार्य के परिणाम में उत्पाद डिजाइन, विश्वसनीयता और गुणवत्ता उद्देश्य शामिल हैं.
चरण 2: उत्पाद डिजाइन और विकास
इस चरण का उद्देश्य उत्पाद डिजाइन को पूरा करना है। यह भी है जहां उत्पाद की व्यवहार्यता का मूल्यांकन खेल में आता है। इस चरण में काम के परिणामों में शामिल हैं:
- पूर्ण डिजाइन की समीक्षा और सत्यापन.
- सामग्री और उपकरण की आवश्यकताओं के विशिष्ट विनिर्देश.
- विफलता संभावनाओं का मूल्यांकन करने के लिए पूर्ण डिजाइन के प्रभाव और विफलता मोड का विश्लेषण.
- उत्पाद प्रोटोटाइप के निर्माण के लिए स्थापित नियंत्रण योजना.
चरण 3: उत्पाद निर्माण प्रक्रिया का डिजाइन और विकास
यह चरण विनिर्माण प्रक्रिया की योजना पर केंद्रित है जो नए या बेहतर उत्पाद का उत्पादन करेगा.
उद्देश्य उत्पाद की विशिष्टताओं और गुणवत्ता और उत्पादन लागत को ध्यान में रखते हुए उत्पादन प्रक्रिया को डिजाइन और विकसित करना है.
यह प्रक्रिया दक्षता बनाए रखते हुए उपभोक्ताओं की अपेक्षित मांग को पूरा करने के लिए आवश्यक मात्रा में उत्पादन करने में सक्षम होनी चाहिए। इस चरण के परिणामों में शामिल हैं:
- प्रक्रिया प्रवाह का एक पूर्ण विन्यास.
- जोखिमों को पहचानने और प्रबंधित करने के लिए पूरी प्रक्रिया के प्रभाव और विफलता मोड का विश्लेषण.
- ऑपरेटिंग प्रक्रिया की गुणवत्ता विनिर्देश.
- उत्पाद की पैकेजिंग और परिष्करण आवश्यकताओं.
चरण 4: प्रक्रिया और उत्पाद सत्यापन
यह विनिर्माण प्रक्रिया और अंतिम उत्पाद को मान्य करने के लिए परीक्षण चरण है। इस चरण के चरणों में शामिल हैं:
- उत्पादन प्रक्रिया की क्षमता और विश्वसनीयता की पुष्टि। इसी तरह, उत्पाद की गुणवत्ता की स्वीकृति की कसौटी.
- परीक्षण उत्पादन का एहसास चलता है.
- उत्पाद परीक्षण लागू किए गए उत्पादन दृष्टिकोण की प्रभावशीलता की पुष्टि करने के लिए.
- अगले चरण पर जाने से पहले आवश्यक समायोजन करें.
चरण 5: लॉन्च, मूल्यांकन और निरंतर सुधार
इस चरण में, बड़े पैमाने पर उत्पादन का शुभारंभ होता है, जिसमें प्रक्रियाओं के मूल्यांकन और सुधार पर जोर दिया जाता है.
इस चरण के स्तंभों में प्रक्रिया भिन्नताओं में कमी, समस्याओं की पहचान, साथ ही निरंतर सुधार का समर्थन करने के लिए सुधारात्मक कार्रवाइयों की शुरुआत है।.
प्रक्रिया दक्षता और गुणवत्ता योजना से संबंधित ग्राहकों की प्रतिक्रिया और डेटा का संग्रह और मूल्यांकन भी है। परिणामों में शामिल हैं:
- एक बेहतर उत्पादन प्रक्रिया, प्रक्रिया विविधताओं को कम करके.
- उत्पाद के वितरण में गुणवत्ता और ग्राहक को सेवा में सुधार.
- ग्राहकों की संतुष्टि में सुधार.
उदाहरण
जहां APQP को शामिल करना है
- गुणवत्ता फ़ंक्शन के कार्यान्वयन का उपयोग करके, ग्राहक की आवाज़ से आवश्यकताओं का विकास.
- परियोजना अनुसूची में एकीकृत उत्पाद गुणवत्ता योजना का विकास.
- उत्पाद डिज़ाइन गतिविधियाँ जो डिज़ाइन को जारी करने से पहले प्रक्रिया डिज़ाइन गतिविधि के लिए विशेष विशेषताओं या कुंजियों को संप्रेषित करती हैं। इसमें नए आकार और भाग, तंग सहिष्णुता और नई सामग्री शामिल हैं.
- परीक्षण योजनाओं का विकास.
- प्रगति को ट्रैक करने के लिए औपचारिक डिजाइन समीक्षा का उपयोग.
- उत्पाद डिजाइन के स्रोत द्वारा दी गई डिजाइन सहिष्णुता के अनुसार, पर्याप्त उपकरण और प्रक्रिया के उपकरण की योजना, अधिग्रहण और स्थापना.
- किसी उत्पाद को बेहतर तरीके से इकट्ठा करने के तरीकों पर विधानसभा और विनिर्माण कर्मियों द्वारा सुझावों का संचार.
- किसी उत्पाद या किसी प्रक्रिया के मापदंडों की कुंजी के लिए पर्याप्त गुणवत्ता नियंत्रण की स्थापना, जो अभी भी संभावित विफलताओं के जोखिम को चलाते हैं.
- वर्तमान भिन्नता को समझने के लिए स्थिरता और विशेष विशेषताओं की क्षमता के अध्ययन का एहसास और इस प्रकार प्रक्रियाओं के सांख्यिकीय नियंत्रण और प्रक्रिया की क्षमता के साथ भविष्य के प्रदर्शन की भविष्यवाणी करना.
जो उद्योग इसका उपयोग करते हैं
फोर्ड मोटर कंपनी ने 1980 के दशक की शुरुआत में अपने आपूर्तिकर्ताओं के लिए पहला उन्नत गुणवत्ता नियोजन नियमावली प्रकाशित की। इसने फोर्ड आपूर्तिकर्ताओं को नए उत्पादों के लिए उपयुक्त रोकथाम और पहचान नियंत्रण विकसित करने में मदद की, इस प्रकार कॉर्पोरेट गुणवत्ता के प्रयासों का समर्थन किया।.
80 के दशक के अंत में, मोटर वाहन उद्योग के मुख्य निर्माताओं ने एपीक्यूपी कार्यक्रमों का उपयोग किया। जनरल मोटर्स, फोर्ड और क्रिसलर ने इसे लागू किया था और फिर देखा कि अपने आपूर्तिकर्ताओं को उत्पाद गुणवत्ता नियोजन सिद्धांतों का एक सामान्य मूल बनाने के लिए एकजुट होने की आवश्यकता है.
यह निर्देश 1990 के दशक के प्रारंभ में स्थापित किए गए थे ताकि यह सुनिश्चित किया जा सके कि एपीक्यूपी प्रोटोकॉल का मानकीकृत प्रारूप में पालन किया गया था.
तीन मोटर वाहन निर्माताओं और अमेरिकन सोसायटी फॉर क्वालिटी कंट्रोल के प्रतिनिधियों ने मोटर वाहन उद्योग के भीतर आपसी हित के विषयों पर एक सामान्य समझ रखने के लिए, गुणवत्ता आवश्यकताओं का एक समूह बनाया।.
इस पद्धति का उपयोग अब प्रगतिशील कंपनियों द्वारा योजना के माध्यम से गुणवत्ता और प्रदर्शन की गारंटी देने के लिए किया जा रहा है.
संदर्भ
- विकिपीडिया, मुक्त विश्वकोश (2018)। उन्नत उत्पाद की गुणवत्ता की योजना। से लिया गया: en.wikipedia.org.
- एनपीडी सॉल्यूशंस (2018)। उन्नत उत्पाद गुणवत्ता योजना। से लिया गया: npd-solutions.com.
- गुणवत्ता-एक (2018)। उन्नत उत्पाद गुणवत्ता योजना (APQP)। से लिया गया: quality-one.com.
- बैट्स (2018)। एपीक्यूपी के 5 चरण: मुख्य आवश्यकताओं का अवलोकन। से लिया गया: cebos.com.
- डेविड इनग्राम (2018)। उन्नत उत्पाद गुणवत्ता योजना। लघु व्यवसाय - Chron.com। से लिया गया: smallbusiness.chron.com.