Toyotismo इतिहास, विशेषताओं, चरणों, फायदे और नुकसान
टॉयटोटिज्मो, टोयोटा उत्पादन प्रणाली (टीपीएस) या लीन मैन्युफैक्चरिंग (कचरे के बिना निर्माण) उत्पादन प्रणालियों पर एक तीन मुख्य प्रतिमान, जो कि कंपनी की प्रारंभिक अवस्था में टोयोटा के आसपास की विशेष परिस्थितियों के जवाब में उत्पन्न हुई थी.
इस अर्थ में, इसकी कई मौलिक अवधारणाएं टोयोटा के लिए पुरानी और अनन्य हैं। दूसरों की जड़ें अधिक पारंपरिक स्रोतों में हैं। इन्हें मोटर वाहन उत्पादन से परे कई और उद्योगों में सर्वश्रेष्ठ प्रथाओं के रूप में अपनाया गया है.
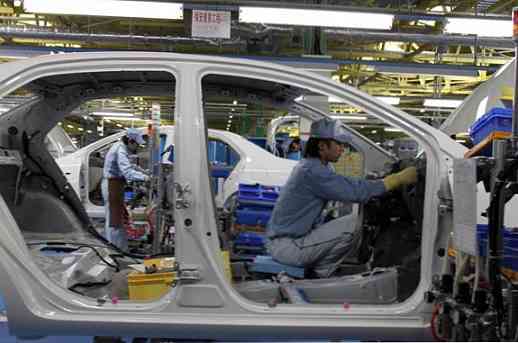
टोयोटा की उत्पादन प्रणाली मुख्य रूप से बड़े पैमाने पर उत्पादन में केंद्रित बड़ी कंपनियों में उपयोग की जाती है। इसकी विशिष्ट विशेषताएं अपशिष्ट प्रबंधन (दुबला प्रबंधन) और अपशिष्ट के बिना उत्पादन (दुबला उत्पादन) हैं.
1990 में, मैसाचुसेट्स इंस्टीट्यूट ऑफ टेक्नोलॉजी द्वारा किए गए एक प्रसिद्ध अध्ययन ने टोयोटा के सफलता के कारकों को स्थापित किया। ये तकनीकी नेतृत्व, लागत नेतृत्व और समय नेतृत्व थे.
कॉर्पोरेट दृष्टिकोण और कंपनी की मूल रणनीति कारखाने को पूर्ण प्रणाली के रूप में मानती है। अर्थात्, एक कार्य प्रणाली जो व्यक्तिगत कार्य स्टेशनों और कार्यशाला को ओवरलैप करती है.
सूची
- 1 इतिहास
- टॉयटोटिस्म के 2 लक्षण
- 3 चरण
- 3.1 एक सरल विनिर्माण प्रणाली का डिजाइन
- 3.2 सुधार के लिए रिक्त स्थान की पहचान
- ३.३ निरंतर सुधार
- 4 फायदे
- ४.१ कचरे को कम करें
- ४.२ दक्षता के लिए देखो
- 4.3 लागत में कमी
- 5 नुकसान
- 5.1 सुधारों का आकलन करना आवश्यक है
- 5.2 स्थिर घटकों के साथ बेहतर काम करता है
- टॉयोटिज्म का इस्तेमाल करने वाली कंपनियों के 6 उदाहरण
- 7 संदर्भ
इतिहास
1902 में, साकिची तोयोदा ने एक करघा का आविष्कार किया था जो जब भी पता चलता है कि एक धागा टूट गया था, तो अपने आप रुक गया। इससे दोषपूर्ण सामग्री के निर्माण को रोका गया.
बाद में, 1924 में, उन्होंने एक स्वचालित करघा बनाया जिसने एक व्यक्ति को कई मशीनों को संचालित करने की अनुमति दी। यह खिलौनावाद की धारणाओं में से एक की उत्पत्ति थी: जिदोका। अवधारणा उत्पादन प्रक्रिया में गुणवत्ता और बहु-प्रक्रिया प्रबंधन के लिए आदमी और मशीन के अलगाव से संबंधित है.
फिर, साकची ने एक ऑटोमोटिव कंपनी बनाई, जिसे उनके बेटे कीचिरो टोयोदा के आरोप में छोड़ दिया गया। 1937 में, किइचिरो ने केवल समय में (समय में) वाक्यांश गढ़ा.
पर्याप्त धन की कमी के कारण, कंपनी उत्पादन में अतिरिक्त उपकरणों या सामग्रियों पर पैसा बर्बाद नहीं कर सकी। सब कुछ समय पर सही होना चाहिए, बहुत जल्दी या बहुत देर से नहीं। यह खिलौनावाद का दूसरा सबसे महत्वपूर्ण उदाहरण बन गया.
द्वितीय विश्व युद्ध के बाद, इंजीनियर ताइची ओहनो को परिचालन उत्पादकता में सुधार करने और बस समय और जिदोका की अवधारणाओं का प्रबंधन करने के लिए सौंपा गया था। उन्हें इंजन प्लांट की मशीन शॉप का मैनेजर नियुक्त किया गया और 1945-1955 के बीच उत्पादन में कई अवधारणाओं के साथ प्रयोग किया गया.
उनका काम और प्रयास काफी हद तक है जो अब टोयोटा प्रोडक्शन सिस्टम के रूप में जाना जाता है.
टोयोटा के लक्षण
टॉयोटिज्म की विशेषताओं में से एक छोटे लॉट का उत्पादन है। प्रक्रिया के प्रत्येक चरण में किए गए कार्य की मात्रा केवल अगले तत्काल चरण की सामग्री की मांग से निर्धारित होती है। यह इन्वेंट्री रखरखाव लागत और वितरण समय को कम करता है.
दूसरी ओर, श्रमिकों को टीमों में प्रशिक्षित किया जाता है। प्रत्येक टीम के पास कई विशिष्ट कार्य करने की जिम्मेदारी और प्रशिक्षण है.
वे मामूली उपकरणों की सफाई और मरम्मत भी करते हैं। प्रत्येक टीम में एक नेता होता है जो लाइन में उनमें से एक के रूप में काम करता है.
इसके अलावा, श्रमिकों को जल्द से जल्द उत्पाद में दोषों की खोज और सुधार करना चाहिए। यदि एक दोष को आसानी से ठीक नहीं किया जा सकता है, तो कोई भी कर्मचारी केबल खींचकर पूरी लाइन को रोक सकता है.
अंत में, आपूर्तिकर्ताओं को भागीदार के रूप में माना जाता है। इन्हें तैयारी के समय, आविष्कारों, दोषों, मशीन के टूटने और अन्य को कम करने के लिए प्रशिक्षित किया जाता है.
चरणों
एक सरल विनिर्माण प्रणाली का डिजाइन
उत्पादन प्रणाली के प्रवाह में रुकावट नहीं होनी चाहिए। यह तब प्राप्त किया जा सकता है जब तैयार उत्पाद में कच्चे माल का तेजी से प्रवाह होता है.
ग्राहक की आवश्यकताओं के अनुसार मैन (ऑपरेटर) और मशीन (उपकरण) को व्यवस्थित रूप से संतुलित होना चाहिए.
सुधार के लिए रिक्त स्थान की पहचान
अंतिम लक्ष्य एक ऐसी प्रणाली है जिसमें ऑपरेटर के मूल्य वर्धित गतिविधियों को अधिकतम करते हुए सामग्री का एक समान प्रवाह होता है.
निरंतर सुधार
टॉयोटिज्म का एक अनिवार्य पहलू उपकरण के लचीलेपन और उत्पाद के लचीलेपन के साथ इसे संरेखित करने की क्षमता है। यह क्लाइंट की आवश्यकताओं के लिए त्वरित रूप से प्रतिक्रिया करने की अनुमति देगा और, एक ही समय में, केवल-इन-टाइम निर्माता होने के लिए।.
लाभ
कचरे को कम करें
टॉयोटिज्म के फायदों में से एक यह है कि यह सभी प्रकार के कचरे को कम से कम करना चाहता है। इसमें भौतिक दोषों से लेकर कार्यकर्ता एर्गोनॉमिक्स तक सब कुछ शामिल है.
दक्षता के लिए देखो
पर्यावरण की स्थिति जो श्रम दक्षता में बाधा डालती है, उससे भी बचा जाता है। कर्मचारी सुधार प्रक्रियाओं में सक्रिय रूप से भाग लेते हैं। यह उनके अपनेपन की भावना को पुष्ट करता है और उनकी प्रेरणा को बढ़ाता है.
लागत में कमी
दूसरी ओर, उचित समय की रणनीति कंपनी के संसाधनों के बेहतर उपयोग की अनुमति देती है। यह नकदी प्रवाह को बढ़ाने में भी मदद करता है। भंडारण की जरूरत कम हो जाती है, इस प्रकार लागत कम हो जाती है.
भंडारण में बचाई गई जगह का उपयोग नई उत्पाद लाइनों को जोड़ने के लिए किया जा सकता है। और ग्राहकों की मांग में बदलाव के लिए कर्मचारियों के पास जल्दी प्रतिक्रिया करने के लिए अधिक समय है.
नुकसान
सुधारों को महत्व देना आवश्यक है
उत्पादकता और कचरे की निगरानी उत्पादन के लिए उपयोग किए जाने वाले समय को प्रभावित कर सकती है। सुधार के मूल्य की जांच की जानी चाहिए। यदि किसी अनुभाग में प्रदर्शन पिछले चरण की तुलना में अधिक होने का प्रबंधन करता है, तो परिणाम बेहतर नहीं हुए हैं.
स्थिर घटकों के साथ सबसे अच्छा काम करता है
समान रूप से, एक और नुकसान यह है कि सिस्टम के स्थिर घटकों के साथ बस-इन-टाइम सिद्धांत सबसे अच्छा काम करते हैं। किसी भी प्रतिबंध की योजना के लिए संभावित रूप से पूरी प्रणाली को खतरे में डालने के लिए जिम्मेदार नहीं है.
टॉयोटिज्म का उपयोग करने वाली कंपनियों के उदाहरण
इस प्रणाली का उपयोग करने वाली कंपनियों का क्लासिक उदाहरण, निश्चित रूप से, टोयोटा कंपनी है। टोयोटा दर्शन ने इसे दुनिया भर में सबसे महत्वपूर्ण मोटर वाहन कंपनियों में से एक बनाने में मदद की है। इस अवधारणा को दुनिया भर में दोहराया गया है.
टॉयोटिज्म की रणनीतियों को लागू करने वाली कंपनियों में से एक जॉन डीरे है। कृषि मशीनरी के इस निर्माता ने 2003 में आयोवा, संयुक्त राज्य अमेरिका में अपने संचालन को बदलने के लिए एक महत्वपूर्ण निवेश किया.
इन प्रथाओं ने उन्हें अतिरिक्त मूल्य के बिना गतिविधियों की पहचान करने और उन्हें यथासंभव दूर करने की अनुमति दी है.
संदर्भ
- हाक, आर। (2003)। अंतर्राष्ट्रीय व्यापार में सामूहिक रणनीतियों का सिद्धांत और प्रबंधन: एशिया में जापानी जर्मन व्यापार सहयोग पर वैश्वीकरण का प्रभाव। न्यूयॉर्क: पालग्रेव मैकमिलन.
- झुक की कला। (एस / एफ)। टोयोटा प्रोडक्शन सिस्टम बेसिक हैंडबुक। Artoflean.com से 7 फरवरी, 2018 को लिया गया.
- 1000 वेंचर्स। (एस / एफ)। टोयोटा प्रोडक्शन सिस्टम (TPS) के 7 सिद्धांत। 7 फरवरी, 2018 को 100000000.com से लिया गया.
- शापक, एस। (एस / एफ)। झुक उत्पादन के लाभ और नुकसान। Smallbusiness.chron.com से 7 फरवरी, 2018 को लिया गया.
- बसाक, डी।; हैदर, टी। और श्रीवास्तव, ए.के. (2013)। आधुनिक संचालन प्रबंधन में झुक विनिर्माण प्रणालियों को प्राप्त करने के लिए रणनीतिक कदम। कंप्यूटर विज्ञान और प्रबंधन अध्ययन के अंतर्राष्ट्रीय जर्नल, वॉल्यूम 13, नंबर 5, पीपी। 14-17.
- वैश्विक विनिर्माण (2014, 11 जून)। शीर्ष 10: दुनिया में दुबला विनिर्माण कंपनियां। Manufacturingglobal.com से 7 फरवरी, 2018 को लिया गया.